RCP2-GR3LS / GR3LM 3 Finger Electric Gripper

RCP2-GR3LS / GR3LM 3 Finger Electric Gripper
|

RCP2-GR3LS 3 Finger Gripper, Lever Type, Actuator Width 62mm, Pulse Motor
RCP2-GR3LM 3 Finger Gripper, Lever Type, Actuator Width 80mm, Pulse Motor
|
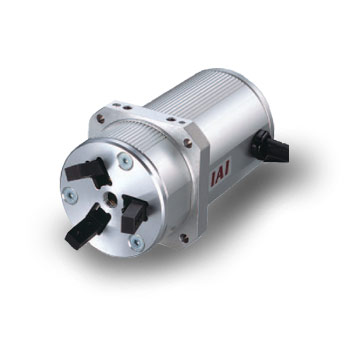
|
RCP2-GR3LS Lead and Load Capacity
Model
|
Gear Ratio (mm)
|
Max Gripping Force (N)
|
Stroke (°)
|
RCP2-GR3LS-I-28P-30-19-P1-[1]-[2] |
30
|
18
|
19
|
[1] = Cable Length, [2] = Options
RCP2-GR3LS Stroke and Maximum Opening/Closing Speed
Gear Ratio
|
Stroke
|
19 (°)
|
30
|
200
|
(Unit: °/s)
RCP2-GR3LS Specs
Item
|
Description
|
Drive Method
|
Worm Gear + Worm Wheel Gear
|
Positioning Repeatability
|
±0.01mm
|
Backlash
|
1° or less per side (Fingers always pressured to open side via spring)
|
Weight
|
0.6kg
|
Ambient Operating Temp/Humidity
|
0-40 °C, 85% RH or below (non-condensing)
|
|
RCP2-GR3LS Options
Name |
Model |
Page |
Shaft Bracket
|
SB
|
|
Flange Bracket
|
FB
|
|
RCP2-GR3LS Correlation Diagram of Speed and Load Capacity
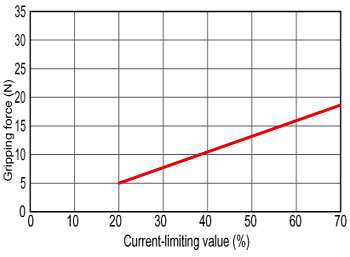
*The values in the graph indicate gripping forces at a gripping point of 10mm. The actual gripping force decreases in inverse proportion to the distance from the opening/closing fulcrum. Calculate the actual gripping force using the following formulas.
Effective gripping force (S type) = P x 24 / (L+14)
Effective gripping force (M type) = P x 28.5 / (L+18.5)
P = Gripping force determined from the graph
L = Distance from the finger attachment surface to the gripping point.
 |
(1) The maximum opening/closing speed indicates the operating speed on one side. The relative operating speed is twice this value.
(2) The maximum gripping force is the sum of gripping forces of both fingers when the gripping point distance is 10 and overhang distance is 0. Refer to the Effective Gripping force formula to determine the work that can be physically transferred. |
|
RCP2-GR3LS Controllers
RCP2 series actuators can be operated using the following controllers.
Choose the type that best suits your specific purpose.
Name
|
Model
|
Features
|
Max Positioning Points
|
Input Power Supply
|
Power Supply Capacity
|
Reference
|
Positioner Type
|
PCON-C-28PI-NP-2-0
|
Supports up to 512 positioning points
|
512 points
|
DC24V
|
2A max.
|
|
Positioner type meeting safety category
|
PCON-CG-28PI-NP-2-0
|
Solenoid Valve Type
|
PCON-CY-28PI-NP-2-0
|
Same control actions as those applicable to solenoid valves
|
3 points
|
Pulse-train Input Type (differential line driver specification)
|
PCON-PL-28PI-NP-2-0
|
Pulse-train input type supporting a differential line driver
|
(-)
|
Pulse-train Input Type (open collector specification)
|
PCON-PO-28PI-NP-2-0
|
Pulse-train input type supporting an open collector
|
Serial Communication Type
|
PCON-SE-28PI-0-0
|
Dedicated serial communication type
|
64 points
|
Program Control Type
|
PSEL-C-1-28PI-NP-2-0
|
Programmable type capable of operating up to 2 axes
|
1500 points
|
|
RCP2-GR3LM Lead and Load Capacity
Model
|
Gear Ratio (mm)
|
Max Gripping Force (N)
|
Stroke (°)
|
RCP2-GR3LM-I-42P-30-19-P1-[1]-[2] |
30
|
51
|
19
|
[1] = Cable Length, [2] = Options
RCP2-GR3LM Stroke and Maximum Opening/Closing Speed
Gear Ratio
|
Stroke
|
19 (°)
|
30
|
200
|
(Unit: °/s)
RCP2-GR3LM Specs
Item
|
Description
|
Drive Method
|
Worm Gear + Worm Wheel Gear
|
Positioning Repeatability
|
±0.01mm
|
Backlash
|
1° or less per side (Fingers always pressured to open side via spring)
|
Weight
|
1.1kg
|
Ambient Operating Temp/Humidity
|
0-40 °C, 85% RH or below (non-condensing)
|
|
RCP2-GR3LM Options
Name |
Model |
Page |
Shaft Bracket
|
SB
|
|
Flange Bracket
|
FB
|
|
RCP2-GR3LM Correlation Diagram of Speed and Load Capacity
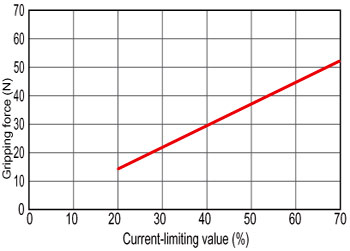
*The values in the graph indicate gripping forces at a gripping point of 10mm. The actual gripping force decreases in inverse proportion to the distance from the opening/closing fulcrum. Calculate the actual gripping force using the following formulas.
Effective gripping force (S type) = P x 24 / (L+14)
Effective gripping force (M type) = P x 28.5 / (L+18.5)
P = Gripping force determined from the graph
L = Distance from the finger attachment surface to the gripping point.
 |
(1) The maximum opening/closing speed indicates the operating speed on one side. The relative operating speed is twice this value.
(2) The maximum gripping force is the sum of gripping forces of both fingers when the gripping point distance is 10 and overhang distance is 0. Refer to the Effective Gripping force formula to determine the work that can be physically transferred. |
|
RCP2-GR3LM Controllers
RCP2 series actuators can be operated using the following controllers.
Choose the type that best suits your specific purpose.
Name
|
Model
|
Features
|
Max Positioning Points
|
Input Power Supply
|
Power Supply Capacity
|
Reference
|
Positioner Type
|
PCON-C-42PI-NP-2-0
|
Supports up to 512 positioning points
|
512 points
|
DC24V
|
2A max.
|
|
Positioner type meeting safety category
|
PCON-CG-42PI-NP-2-0
|
Solenoid Valve Type
|
PCON-CY-42PI-NP-2-0
|
Same control actions as those applicable to solenoid valves
|
3 points
|
Pulse-train Input Type (differential line driver specification)
|
PCON-PL-42PI-NP-2-0
|
Pulse-train input type supporting a differential line driver
|
(-)
|
Pulse-train Input Type (open collector specification)
|
PCON-PO-42PI-NP-2-0
|
Pulse-train input type supporting an open collector
|
Serial Communication Type
|
PCON-SE-42PI-0-0
|
Dedicated serial communication type
|
64 points
|
Program Control Type
|
PSEL-C-1-42PI-NP-2-0
|
Programmable type capable of operating up to 2 axes
|
1500 points
|
|
Please refer to ROBO Cylinder General Catalog
Do you have any questions or comments about our products? Contact Us
Go to:
 |