Caution when Using a Guide with a Rod Type
Rod type actuators are classified into two main categories of “Radial cylinder type” and “Anti-rotation” type. Depending on the type, methods for dealing with radial loads and cautionary notes will be different, as indicated below.
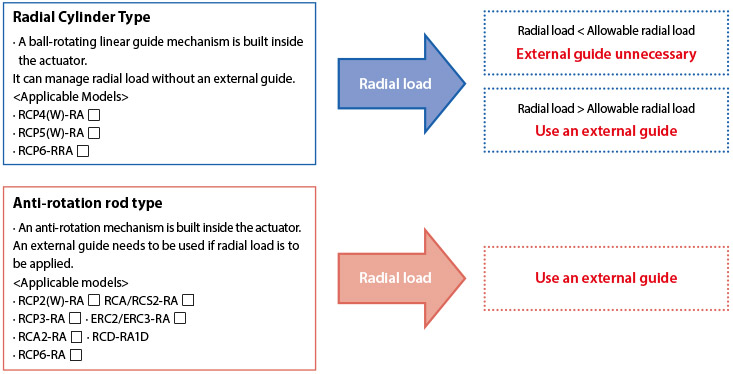
● Parallelism of the actuator and the external guide
When using an external guide, if there is a deviation in the level of parallelism between the actuator and the external guide (either the horizontal or vertical surfaces), operation defects or early actuator damage may occur.
When the external guide is attached, adjustments have to be made to align the actuators and the guides. Then the uniformity of the sliding resistance throughout the entire stroke has to be checked.
This is done by checking the uniformity of the current value through the current monitoring function of the controller.
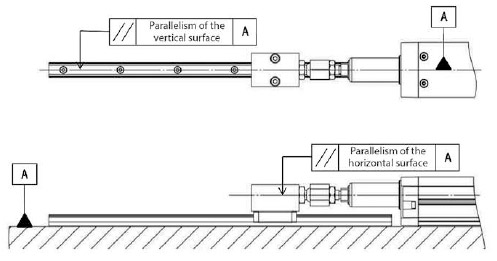
● External guide mounting method
The method for mounting the external guide differs by type.
Even if the parallelism between the guide and the actuator could be adjusted, please be careful as there is a danger of accidental damage of the actuator with the incorrect mounting method.
Radial Cylinder type
For mounting the external guide for a radial cylinder type, a floating joint mount is recommended.
The floating joint compensates for the deviation in the parallelism of the built-in guide and the external guide, and this makes adjustments easy.
With rigid mounting, adjusting the parallelism of the built-in guide and the external guide is difficult, and even a slight deviation causes stress on the guide and can lead to early damaging.
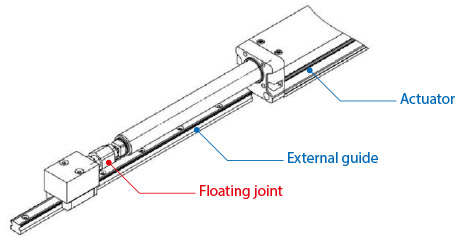
Anti-rotation rod type
For mounting the external guide for an anti-rotation rod type, rigid mounting is recommended. Since the anti-rotation rod type cannot handle force in the rod rotation direction, it is necessary to regulate the rod rotation direction.
The rod rotation direction is not regulated with the floating joint, so force in the rod rotation direction could be applied to the anti-rotation mechanism during actuator operation, and this could cause early wearing of the anti-rotation mechanism. (There is no problem if it is a floating joint whose direction of rotation is regulated.)
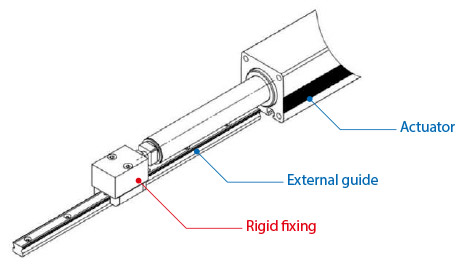