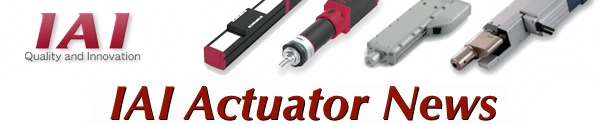
We have a new Easy Automation Application Improvement video Vol.8-1.
Easy Automation Improvement Example Vol.8-1
Inspection System for Resin Case Insert Parts
Inspects the condition, position and quantity of two types of insert parts installed in large onboard resin cases. Formed parts are placed and removed from the system by an operator.
Problems when Air Cylinders are used
The formed part and camera must be stationary to capture a stable inspection image. The camera can capture a clear image after the vibration of the stopping table and camera has died down.
This system has to stand by for 1 second after the movement stops to wait for the vibration to die down.
We could try to lower the air cylinder speed to suppress the vibration caused by the stopping shock. Unfortunately, this would increase the travel time.
So we are not able to shorten the cycle time with the air cylinder.
Currently, it takes 20.0 seconds to inspect one part.
Breakdown
- Time needed for the operator to change and screen parts: 10.0 seconds
- Time from start to end of the inspection system: 10.0 seconds
Improvements Achieved by the ROBO Cylinder®
1. Shorter standby time through optimization of operating conditions
Substantially shorter line operating hours
By setting the deceleration low and the speed and acceleration high, high-speed movement free from shock or vibration became possible.
As a result, the work and camera now move faster and spend less time standing by after moving. The inspection time was reduced by 5 seconds.
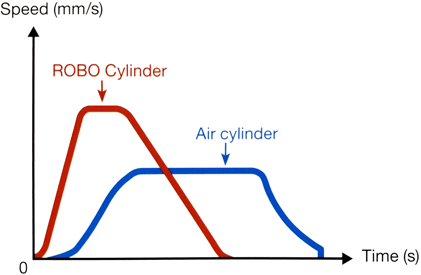
The shorter inspection time resulted in substantially shorter system operating hours.
Inspection time(Per part: Time needed for the operator to change and screen parts + Time from start to end of the inspection system) |
|
Air cylinder: 20.0 seconds |
ROBO Cylinder: 15.0 seconds |
Line operating hours a day |
|
Air cylinder: 11.7 hours |
ROBO Cylinder: 8.8 hours |
Line operating hours a year |
|
Air cylinder: 2,925 hours |
ROBO Cylinder: 2,200 hours |
2. Simpler System Configuration
The elimination of external guides made quick assembly and adjustment possible and also simplified the system configuration.
The newly adopted RCP6-WSA (wide slider type) actuator is slim and withstands high load moment. Two motor installation specifications are available to choose from: the coupled type and the side-mounted type.
Cost Cutting Effect
(1) Conditions
Required inspection capacity | 2,100 pieces/day |
Annual operating days | 250 days |
Labor cost | $18*/hour |
(2) Comparison of Air Cylinder and ROBO Cylinder®
Item | System using air cylinder | System using ROBO Cylinder | |
Modification cost | - | Total cost: $5,000* (including additional peripherals) |
|
Inspection time | 20.0 seconds/unit | 15.0 seconds/unit | |
Line operating hours | 11.7 hours/day | 8.8 hours/day | |
Labor cost | $52,650*/year 11.7 hours x $18* x 250 days = $52,650* |
$39,600*/year 8.8 hours x $18* x 250 days = $39,600* |
(3) Cost Cutting Effect
Air cylinder | ROBO Cylinder | ||
Labor Cost (annual) | $52,650* - | $39,600* = | $13,050* |
Difference = | $13,050* |
Result
By implementing the ROBO Cylinder®,
the line operating hours decreased by 2.9 hours a day.
$13,050* of annual cost savings was achieved.
Please call IAI America from 8:30 am to 5:00 pm at these locations:
Eastern U.S. office: (678) 354-9470
Central U.S. office: (800) 944-0333
Western U.S. office: (800) 736-1712
Outside office hours, please use our contact form.