NS-MXMMA
*Note: Some pictures on this page are still Japanese version and the English version pictures are coming soon.
Main Specifications
item | Contents | |||
---|---|---|---|---|
Lead | Ball screw lead (mm) | 30 | 20 | |
Horizontal | Payload capacity | Maximum payload (kg) | 25 | 40 |
Speed/Acceleration | Maximum speed (mm/s) | 1800 | 1200 | |
Rated acceleration/deceleration (G) | 0.3 | 0.3 | ||
Maximum acceleration/deceleration (G) | 1 | 0.8 | ||
vertical | Payload capacity | Maximum payload (kg) | - | - |
Speed/Acceleration | Maximum speed (mm/s) | - | - | |
Rated acceleration/deceleration (G) | - | - | ||
Maximum acceleration/deceleration (G) | - | - | ||
Thrust | Rated thrust (N) | 113.9 | 170.9 | |
brake | Brake specifications | - | - | |
Brake holding force (kgf) | - | - | ||
stroke | Minimum stroke (mm) | 300 | 300 | |
Maximum stroke (mm) | 1500 | 1500 | ||
Stroke pitch (mm) | 50 | 50 |
item | Contents |
---|---|
Drive system | Ball screw φ16mm Rolled C5 equivalent |
Repeated positioning accuracy | ±0.01mm |
Lost Motion | 0.02mm以下 |
Base | Material: Aluminum with white anodized coating |
Linear Guide | Linear infinite circulation type |
Static allowable moment | Ma:227N・m |
Mb:325N・m | |
Mc:531N・m | |
Dynamic allowable moment (注2) |
Ma:81.0N・m |
Mb:116N・m | |
Mc:189N・m | |
Operating ambient temperature and humidity | 0 to 40°C, below 85% RH (without condensation) |
Protection rating | - |
Vibration and Shock Resistance | 4.9m/s2 |
International Standards Compliance | CE Mark, RoHS Directive |
Motor Type | AC Servo Motor |
Encoder Type | Incremental / Absolute |
Encoder Pulse Count | 16384 pulse/rev |
Delivery Time | Please refer to the [Delivery Inquiry] on the website for more information. |
(Note 2) This is based on a standard rated lifespan of 10,000 km. The operational lifespan may vary depending on the operating conditions and installation setup.
1-244Please check the operating lifespan on the webpage.
Slider type moment direction

Payload table by speed/acceleration
The unit of payload is kg. Blank spaces mean the item cannot be operated.
posture | Horizontal | vertical | |||||||||||||||||||||
---|---|---|---|---|---|---|---|---|---|---|---|---|---|---|---|---|---|---|---|---|---|---|---|
Lead (mm) |
Maximum speed (mm/s) |
Acceleration (G) | |||||||||||||||||||||
0.2 | 0.3 | 0.4 | 0.5 | 0.6 | 0.7 | 0.8 | 0.9 | 1.0 | 1.1 | 1.2 | 0.2 | 0.3 | 0.4 | 0.5 | 0.6 | 0.7 | 0.8 | 0.9 | 1.0 | 1.1 | 1.2 | ||
30 | 1800 | 25 | 25 | 16 | 10 | 6 | 3.5 | 2 | 1 | 0.5 | For horizontal use only. | ||||||||||||
20 | 1200 | 40 | 40 | 28 | 18 | 10 | 5 | 2.5 |
Stroke and maximum speed
(Unit: mm/s)
stroke Lead |
300 to 1500 (every 50 mm) |
---|---|
30 | 1800 |
20 | 1200 |
Adaptive Controller
The actuators on this page can be operated with the following controllers. Please select the type that suits your application.
name | exterior | Maximum number of connectable axes |
Power supply voltage | Control Method | Maximum number of positioning points | ||||||||||||||
---|---|---|---|---|---|---|---|---|---|---|---|---|---|---|---|---|---|---|---|
Positioner | Pulse train | program | Network ※Select | ||||||||||||||||
DV | CC | CIE | PR | CN | ML | ML3 | EC | EP | PRT | SSN | ECM | ||||||||
RCON | ![]() |
16 (ML3, SSN, ECM are 8) |
DC24V Single-phase AC200V Three-phase AC200V |
- | - | - | ● | ● | ● | ● | - | - | ● | ● | ● | ● | ● | ● | 128 (ML3, SSN, ECM no position data) |
RSEL | ![]() |
8 | - | - | ● | ● | ● | ● | ● | - | - | - | ● | ● | ● | - | - | 36000 | |
SCON-CB/CGB | ![]() |
1 | Single phase AC 100V/200V |
● | ● | - | ● | ● | ● | ● | ● | ● | ● | ● | ● | ● | - | ● | 512 (network specification is 768) |
SSEL-CS | ![]() |
2 | ● | - | ● | ● | ● | - | ● | - | - | - | - | ● | - | - | - | 20000 | |
XSEL-P/Q | ![]() |
6 | Single-phase AC200V Three-phase AC200V |
- | - | ● | ● | ● | - | ● | - | - | - | - | ● | - | - | - | 20000 |
XSEL-RA/SA | ![]() |
8 | - | - | ● | ● | ● | - | ● | - | - | - | ● | ● | - | - | - | 55000 (varies by type) |
(Note) For network abbreviations such as DV and CC, please see page 8-17 .
(Note) The multi-slider is controlled by a 2-axis controller or two SCONs.
(Note) Absolute actuators cannot be connected to RCON-SC.
International Standards
Selection considerations
![]() |
(1) The "main spec" payload capacity shows the maximum value. For details, refer to the "Table of payload capacity by speed and acceleration". (2) The "main spec" maximum payload capacity is the value when operating at the maximum speed. (3) Caution is required depending on the installation position. For details, refer to page 1-261 . (4) If you wish to position the cable bear on the opposite side, rotate the main body 180 degrees before installing. (5) The guideline for the overhang load length is 600 mm or less in the Ma, Mb, and Mc directions. |
Dimensions
ST: Stroke
ME: Mechanical end
(Note) The motor cable and encoder cable are connected to the cable joint connector.
For cable details, see page 1-114 .
(Note) When performing origin return, the slider will move to the ME, so please be careful not to interfere with the surroundings.
(Note) The gap between the outer diameter of the cables/hoses stored in the cable carrier and the inner wall, as well as the gap between the cables/hoses themselves, should be 2 mm or more.
(Note) The cables and hoses stored in the cable bear must have an outer diameter of φ12 or less, be arranged horizontally, and not cross each other.
(Note) Please note that if the number of cables/hoses stored in the cable carrier exceeds the above specifications, undue stress will be applied to the cables, significantly shortening their lifespan.
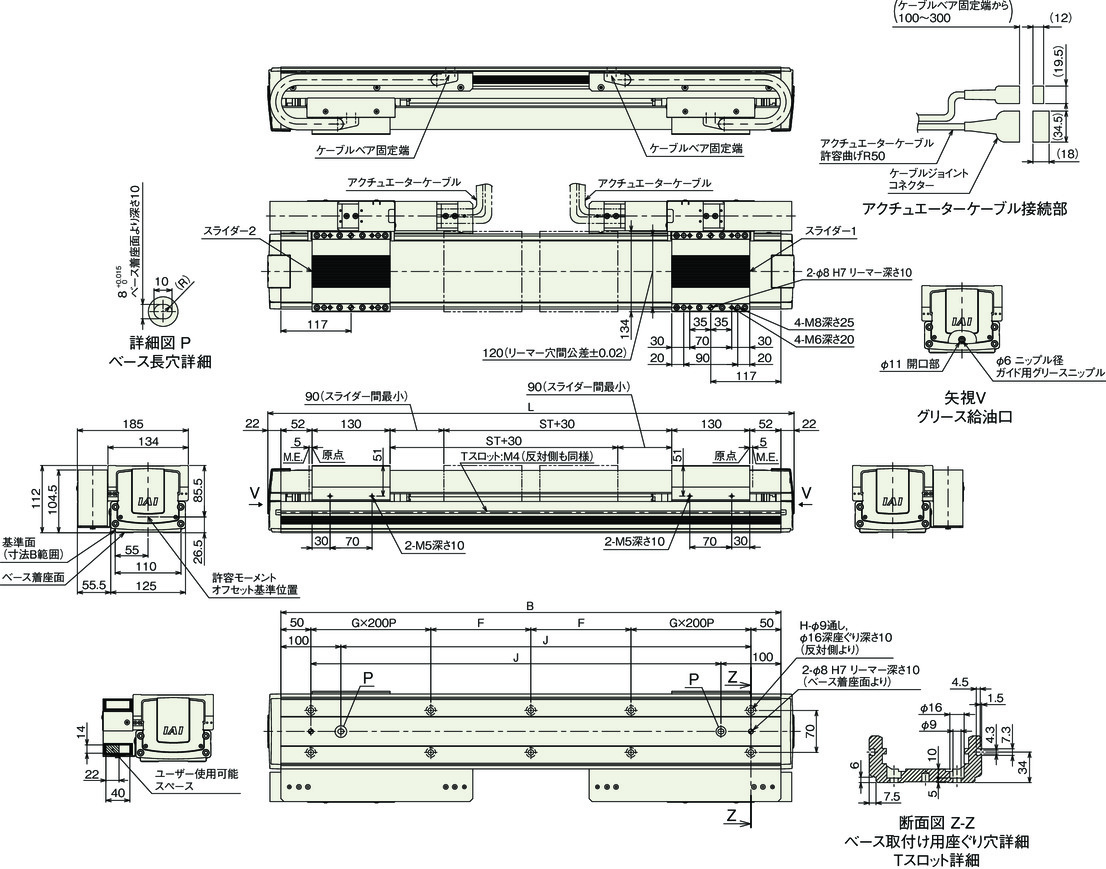
Stroke dimensions
stroke | 300 | 350 | 400 | 450 | 500 | 550 | 600 | 650 | 700 | 750 | 800 | 850 | 900 | 950 | 1000 | 1050 | 1100 | 1150 | 1200 | 1250 | 1300 | 1350 | 1400 | 1450 | 1500 |
---|---|---|---|---|---|---|---|---|---|---|---|---|---|---|---|---|---|---|---|---|---|---|---|---|---|
L | 828 | 878 | 928 | 978 | 1028 | 1078 | 1128 | 1178 | 1228 | 1278 | 1328 | 1378 | 1428 | 1478 | 1528 | 1578 | 1628 | 1678 | 1728 | 1778 | 1828 | 1878 | 1928 | 1978 | 2028 |
B | 784 | 834 | 884 | 934 | 984 | 1034 | 1084 | 1134 | 1184 | 1234 | 1284 | 1334 | 1384 | 1434 | 1484 | 1534 | 1584 | 1634 | 1684 | 1734 | 1784 | 1834 | 1884 | 1934 | 1984 |
F | 142 | 167 | 192 | 217 | 242 | 267 | 292 | 317 | 142 | 167 | 192 | 217 | 242 | 267 | 292 | 317 | 142 | 167 | 192 | 217 | 242 | 267 | 292 | 317 | 142 |
G | 1 | 1 | 1 | 1 | 1 | 1 | 1 | 1 | 2 | 2 | 2 | 2 | 2 | 2 | 2 | 2 | 3 | 3 | 3 | 3 | 3 | 3 | 3 | 3 | 4 |
H | 10 | 10 | 10 | 10 | 10 | 10 | 10 | 10 | 14 | 14 | 14 | 14 | 14 | 14 | 14 | 14 | 18 | 18 | 18 | 18 | 18 | 18 | 18 | 18 | twenty two |
J | 634 | 684 | 734 | 784 | 834 | 884 | 934 | 984 | 1034 | 1084 | 1134 | 1184 | 1234 | 1284 | 1334 | 1384 | 1434 | 1484 | 1534 | 1584 | 1634 | 1684 | 1734 | 1784 | 1834 |
Mass by stroke
stroke | 300 | 350 | 400 | 450 | 500 | 550 | 600 | 650 | 700 | 750 | 800 | 850 | 900 | 950 | 1000 | 1050 | 1100 | 1150 | 1200 | 1250 | 1300 | 1350 | 1400 | 1450 | 1500 |
---|---|---|---|---|---|---|---|---|---|---|---|---|---|---|---|---|---|---|---|---|---|---|---|---|---|
Mass (kg) | 15.6 | 16.2 | 16.8 | 17.4 | 18.0 | 18.6 | 19.3 | 19.9 | 20.5 | 21.1 | 21.7 | 22.3 | 22.9 | 23.6 | 24.2 | 24.8 | 25.4 | 26.0 | 26.6 | 27.2 | 27.9 | 28.5 | 29.1 | 29.7 | 30.3 |