IXA-3NNN1805
IXA-4NNN1805
*Note: Some pictures on this page are still Japanese version and the English version pictures are coming soon.
Main Specifications
item | Contents | |||
---|---|---|---|---|
3-axis specifications | 4-axis specifications | |||
Maximum payload (kg) (Note 1) | 1 | |||
Speed (Note 2) |
Combined maximum speed (mm/s) | 2638 | ||
Maximum speed of each axis | First arm (deg/s) | 540 | ||
Second Arm (deg/s) | 540 | |||
Vertical axis (mm/s) | 850 | |||
Axis of rotation (deg/s) | - | 1600 | ||
Press (N) (Note 3) | upper limit | 40 | ||
lower limit | 5 | |||
Arm length (mm) | 180 | |||
Arm length of each axis (mm) | First Arm | 80 | ||
Second Arm | 100 | |||
Each axis motion range | First Arm (degrees) | ±125 | ||
Second Arm (degrees) | ±145 | |||
Vertical axis (mm) | 50 | |||
Rotation axis (degrees) | - | ±360 |
item | Contents | ||
---|---|---|---|
3-axis specifications | 4-axis specifications | ||
Position repeatability (Note 4) |
In the horizontal plane | ±0.01mm | |
Vertical axis | ±0.01mm | ||
Rotation axis | - | ±0.01 degrees | |
User wiring | 10 cores (9 cores + shield) AWG25 (rated 30V/MAX1A) | ||
User piping | Outer diameter φ4 Inner diameter φ2.5 Air tube x 2 (Maximum operating pressure 0.6MPa) |
||
LED indicator light (Note 5) | 1 small amber LED indicator light (24V DC supply required) | ||
Brake release switch (Note 6) | Brake release switch to prevent vertical axis from falling | ||
Tip Shaft | Permissible Torque | 0.35N・m | 0.35N・m |
Allowable load moment | 0.5N・m | ||
Ambient temperature and humidity | 0 to 40°C, 20 to 85% RH or less (no condensation) | ||
Protection rating | IP20 | ||
Vibration and shock resistance | No shock or vibration | ||
Noise (Note 7) | 80dB or less | ||
Overseas compatible standards | CE mark, RoHS directive | ||
Motor Type | AC servo motor | ||
Motor capacity | First Arm | 50W | |
Second Arm | 50W | ||
Vertical axis | 50W | ||
Rotation axis | - | 50W | |
Encoder Type | Battery-less absolute | ||
Encoder Pulse Number | 16384 pulses/rev | ||
deadline | Listed on the website [Delivery Date Inquiry] |
Correlation diagram between pressing force and current limit value (reference value)
This is the pressing force at the tip of the vertical axis. (Note 3)
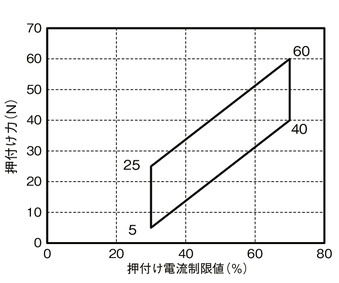
Adaptive Controller
The actuators on this page can be operated with the following controllers. Please select the type that suits your application.
name | exterior | Maximum number of connectable axes |
Power supply voltage | Control Method | Maximum number of positioning points | ||||||||||||||
---|---|---|---|---|---|---|---|---|---|---|---|---|---|---|---|---|---|---|---|
Positioner | Pulse train | program | Network ※Select | ||||||||||||||||
DV | CC | CIE | PR | CN | ML | ML3 | EC | EP | PRT | SSN | ECM | ||||||||
XSEL-RAX/SAX | ![]() |
8 | Three-phase AC200V | - | - | ● | ● | ● | ● | ● | - | - | - | ● | ● | - | - | - | 36666 (varies by type) |
(Note) For network abbreviations such as DV and CC, please see page 8-15 .
(Note) Up to a maximum of SCARA + 4-axis robots can be controlled.
International Standards
Selection considerations
![]() |
(1) For (Note 1) to (Note 9), please refer to page 5-871 . (2) The maximum setting value of acceleration/deceleration varies depending on the mass of the transported object, the travel distance, and the location. In addition, continuous operation at the maximum setting value may cause an overload error. When performing continuous operation, lower the acceleration/deceleration value or set a stop time after acceleration/deceleration referring to the duty ratio (guideline). (3) An absolute reset is required when replacing a motor, etc. An adjustment jig is required to perform an absolute reset on the rotating axis. For details, please refer to page 5-864 . (4) SCARA robots cannot be operated continuously at 100% speed and acceleration. For the operating conditions, please refer to "Guideline for Acceleration/Deceleration Settings". (5) When switching the arm system, the arm will extend in a straight line once, so please be careful of interference with peripheral devices. |
Dimensions
ST: Stroke
ME: Mechanical end
SE: Stroke end
(Note) For cable connections, see page 5-871 (Note 9).
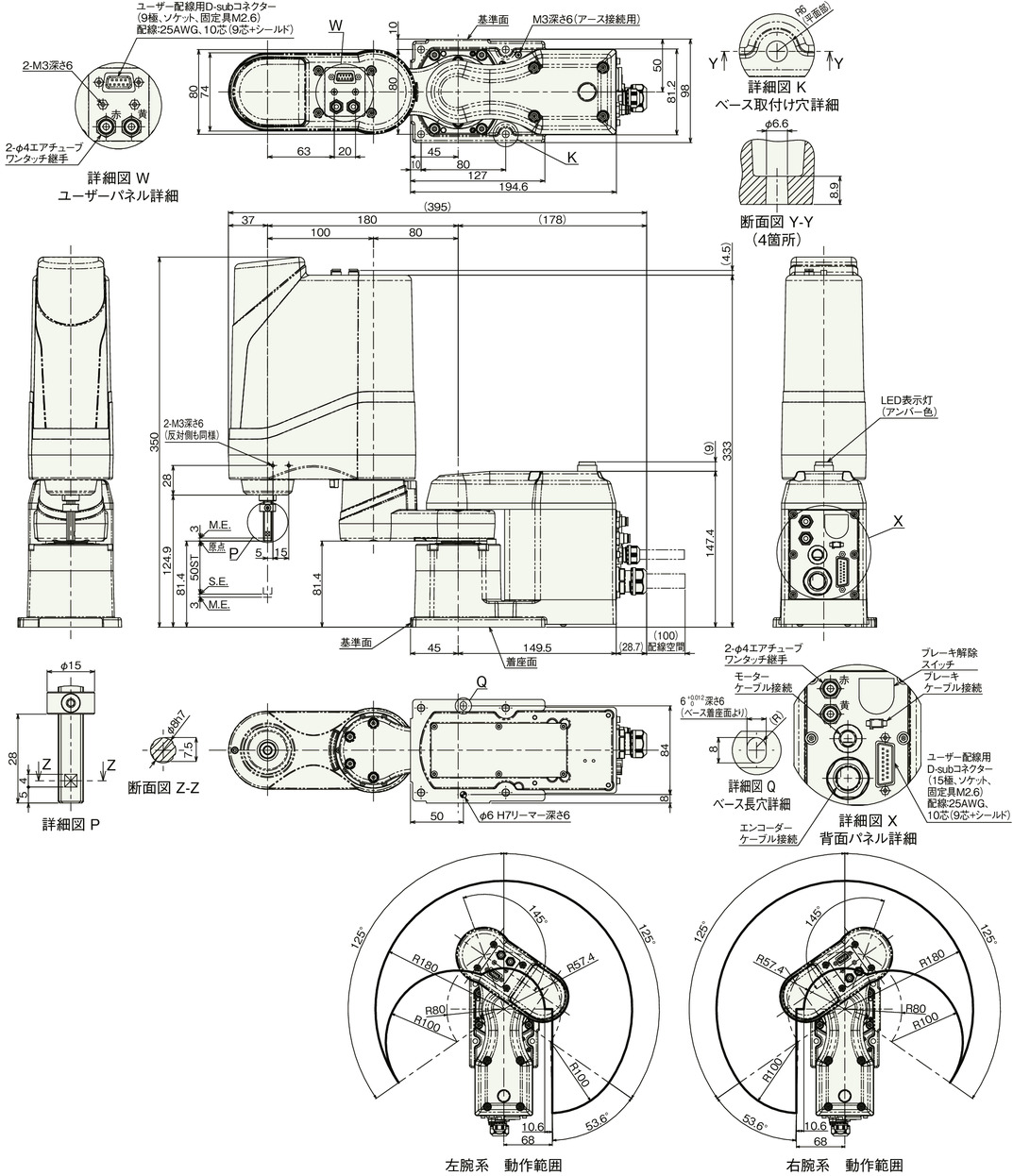
mass
item | Contents | |
---|---|---|
mass | 3-axis specifications | 5.8kg |
4-axis specifications | 6.2kg |
Cycle Time
item | time |
---|---|
Standard Cycle Time | 0.26 seconds |
Continuous Cycle Time | 0.45 seconds |
Standard/continuous cycle time indicates the time required when operating at the fastest round trip operation setting under the conditions below.
0.2 kg transport, vertical movement 25 mm, horizontal movement 100 mm (coarse positioning arch motion)
[Standard cycle time]
This is the time required for maximum speed operation. Generally, this is a guide to high speed performance. Please note that continuous operation at maximum speed is not possible.
[Continuous cycle time]
This is the cycle time for continuous operation.

Allowable moment of inertia of tip shaft
Number of axes | Allowable moment of inertia of tip shaft |
---|---|
3-axis specifications | 0.004 kg m2 |
4-axis specifications |
This is the allowable moment of inertia converted from the center of the tip axis of a SCARA robot (3-axis specifications: vertical axis, 4-axis specifications: rotational axis).
The offset from the center of the tip axis to the center of gravity of the tool must be within the following values.
If the tool center of gravity is moved away from the center of the tip of the shaft, the speed and acceleration must be reduced appropriately. The extension length is limited by the load and operating conditions.
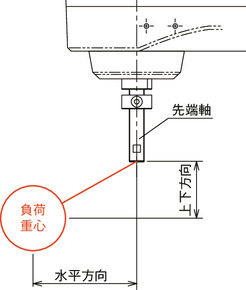
Horizontal | vertical direction |
---|---|
Less than 30mm | Less than 20mm |
Acceleration/deceleration setting guideline
The SCARA Robot IXA cannot be operated continuously at the maximum acceleration/deceleration and maximum speed in the catalog. When operating at the maximum acceleration/deceleration, set the stop time by referring to the continuous operation duty ratio guideline graph. If continuous operation is required, operate the robot at an acceleration/deceleration setting within the continuous operation guideline range in the acceleration/deceleration setting guideline graph.
(1) For PTP operation, be sure to use the WGHT command in the program to set the mass and moment of inertia before operating. For SCARA, the maximum acceleration/deceleration that can be operated with each payload is set to 100%. Please note that even with the same acceleration/deceleration and speed settings, if the payload is different, the operation time will also differ.
(2) Adjust the acceleration/deceleration setting by gradually increasing it from the continuous operation guideline value.
(3) If an overload error occurs, reduce the acceleration/deceleration as appropriate, or adjust the stopping time based on the guideline for the continuous operation duty ratio.
(4) Duty ratio (%) = (operating time / (operating time + stopped time)) x 100
(5) When you want to move the robot horizontally at high speed, try to operate the vertical axis as close to the upper end as possible.
(6) Keep the moment of inertia and payload below the allowable values.
(7) The transport load indicates the moment of inertia about the center of the rotating shaft and the mass.
(8) When operating the robot, observe the appropriate acceleration and deceleration according to the robot's mass and moment of inertia. Failure to observe this may result in premature end of life, damage or vibration of the drive unit.
(9) If the load has a large moment of inertia, vibration may occur in the vertical axis depending on the position of the vertical axis. If vibration occurs, reduce the acceleration/deceleration as appropriate.
PTP Operation
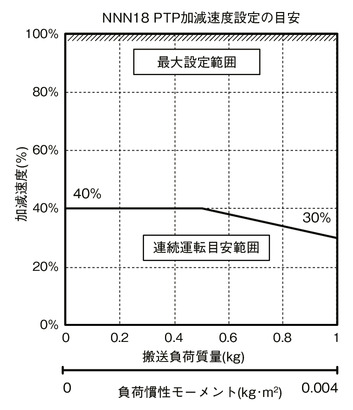
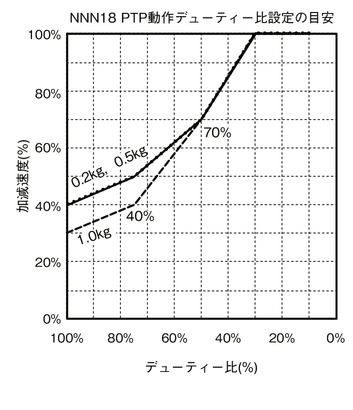
CP operation
Horizontal
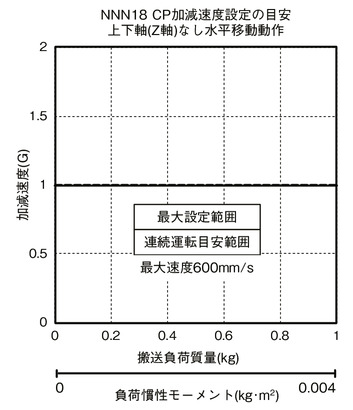
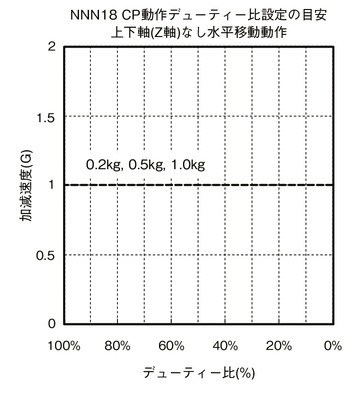
Up and down
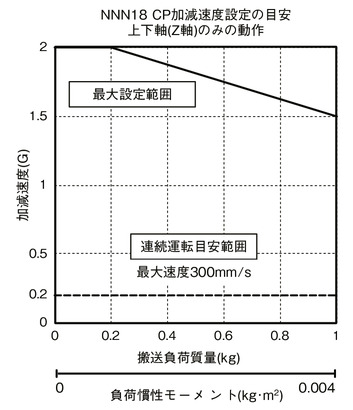
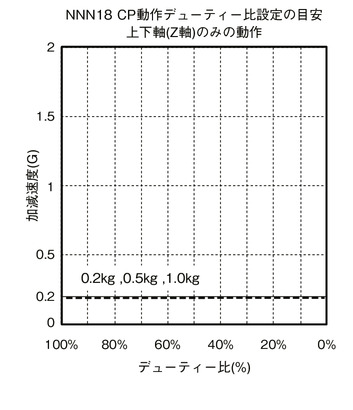
CP operation speed/acceleration/deceleration limit
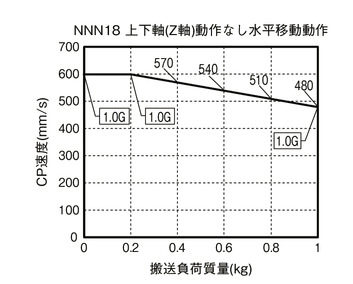
