EC-TC3
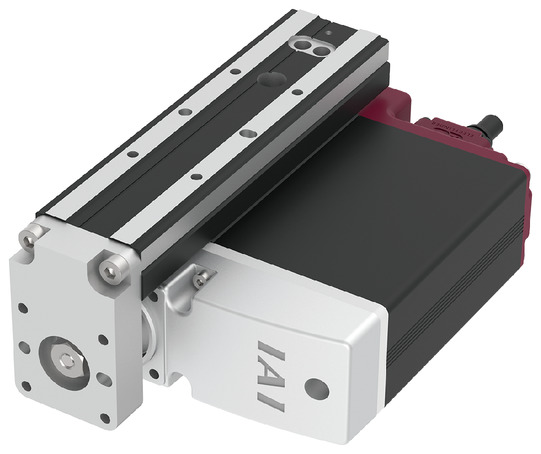
(Note) The photo above shows the table left mounting specification (GT4).
*Note: Some pictures on this page are still Japanese version and the English version pictures are coming soon.
Main Specifications
item | Contents | ||||
---|---|---|---|---|---|
Lead | Ball screw lead (mm) | 6 | 4 | 2 | |
Horizontal | Payload capacity | Maximum payload (kg) | 1.5 | 3 | 6 |
Speed/Acceleration | Maximum speed (mm/s) | 300 | 200 | 75 | |
Minimum speed (mm/s) | 8 | 5 | 3 | ||
Rated acceleration/deceleration (G) | 0.3 | 0.3 | 0.3 | ||
Maximum acceleration/deceleration (G) | 0.3 | 0.3 | 0.3 | ||
vertical | Payload capacity | Maximum payload (kg) | 0.5 | 1 | 2 |
Speed/Acceleration | Maximum speed (mm/s) | 200 | 150 | 75 | |
Minimum speed (mm/s) | 8 | 5 | 3 | ||
Rated acceleration/deceleration (G) | 0.3 | 0.3 | 0.3 | ||
Maximum acceleration/deceleration (G) | 0.3 | 0.3 | 0.3 | ||
Pressing | Maximum thrust when pressing (N) | 14 | twenty one | 42 | |
Maximum pressing speed (mm/s) | 20 | 20 | 5 | ||
brake | Brake specifications | Non-excitation electromagnetic brake | |||
Brake holding force (kgf) | 0.5 | 1 | 2 | ||
stroke | Minimum stroke (mm) | 30 | 30 | 30 | |
Maximum stroke (mm) | 50 | 50 | 50 | ||
Stroke pitch (mm) | 20 | 20 | 20 |
item | Contents |
---|---|
Drive system | Ball screw φ6mm rolled C10 |
Repeated positioning accuracy | ±0.02mm |
Lost Motion | - (Cannot be indicated due to two-point positioning function.) |
Static allowable moment | Ma: 1.81 N・m |
Mb: 2.58 N・m | |
Mc: 4.34 N・m | |
Dynamic allowable moment (Note 10) |
Ma: 0.509 N・m |
Mb: 0.728 N・m | |
Mc: 1.22 N・m | |
Running life | 5000km |
Ambient temperature and humidity | 0 to 40°C, 85% RH or less (no condensation) |
Protection rating | - |
Vibration and shock resistance | 4.9m/ s2 |
Overseas compatible standards | CE mark, RoHS directive |
Motor Type | Pulse motor (□20) (power capacity: maximum 1.25A) |
Encoder Type | Incremental/Battery-less Absolute |
Encoder Pulse Number | 16384 pulses/rev |
deadline | Listed on the website [Delivery Date Inquiry] |
(Note 10) Based on a standard rated life of 5,000 km. The running life will vary depending on the operating conditions and installation. Please check the running life on page 1-276 .
Table type moment direction

Payload table by speed/acceleration
Standard grease specifications. The unit of payload is kg. Blank spaces indicate that the product cannot be operated.
posture | Horizontal | vertical |
---|---|---|
speed | Acceleration (G) | |
(mm/s) | 0.3 | 0.3 |
0 | 1.5 | 0.5 |
50 | 1.5 | 0.5 |
100 | 1.5 | 0.5 |
150 | 1.5 | 0.2 |
200 | 1.5 | 0.2 |
250 | 1 | |
300 | 0.2 |
posture | Horizontal | vertical |
---|---|---|
speed | Acceleration (G) | |
(mm/s) | 0.3 | 0.3 |
0 | 3 | 1 |
50 | 3 | 1 |
100 | 3 | 0.5 |
150 | 1 | 0.2 |
200 | 0.5 |
posture | Horizontal | vertical |
---|---|---|
speed | Acceleration (G) | |
(mm/s) | 0.3 | 0.3 |
0 | 6 | 2 |
twenty five | 6 | 2 |
50 | 4 | 1 |
75 | 0.5 | 0.5 |
If the ambient temperature is below 5°C, use the product at or below the speeds listed below.
・Lead 6: 200mm/s or less
・Lead 4: 150mm/s or less
・Lead 2: 50mm/s or less
Food grade grease specifications. The unit of payload is kg. Blank spaces indicate that the product cannot be operated.
posture | Horizontal | vertical |
---|---|---|
speed | Acceleration (G) | |
(mm/s) | 0.3 | 0.3 |
0 | 1.5 | 0.5 |
50 | 1.5 | 0.5 |
100 | 1.5 | 0.5 |
150 | 1.5 | 0.2 |
200 | 1 |
posture | Horizontal | vertical |
---|---|---|
speed | Acceleration (G) | |
(mm/s) | 0.3 | 0.3 |
0 | 3 | 1 |
50 | 3 | 1 |
100 | 3 | 0.3 |
posture | Horizontal | vertical |
---|---|---|
speed | Acceleration (G) | |
(mm/s) | 0.3 | 0.3 |
0 | 6 | 2 |
twenty five | 6 | 2 |
50 | 1.5 | 0.5 |
75 | 0.5 |
Stroke and maximum speed
(Unit: mm/s)
Lead (mm) |
30 (mm) |
50 (mm) |
---|---|---|
6 | 300<200> | |
4 | 200<150> | |
2 | 75 |
(Note) < > indicates vertical use.
Correlation diagram between pressing force and current limit value
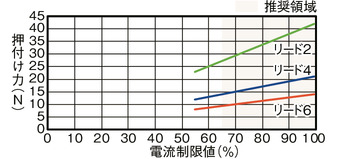
Precautions when performing pressing operation
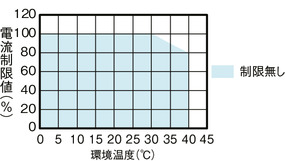
During high thrust pressing operations in high temperature environments,
Please use within the limits shown in the graph.
Adaptive Controller
(Note) The EC series has a built-in controller. For details on the built-in controller, see page 2-769 .
International Standards
Selection considerations
![]() |
(1) The payload in the "Main Specifications" is the maximum value. For details, refer to the "Payload Capacity by Speed and Acceleration Table." (2) When performing a push operation, refer to the "Correlation Diagram of Push Force and Current Limit Value." The push force is a guideline value. For points to note, see page 1-315 . (3) Be sure to select the option symbol from the option price list for the table mounting direction. (4) The guideline for the overhang load length is 50 mm or less in the Ma, Mb, and Mc directions. For details on the overhang load length, see the explanation on page 2-109 . |
Dimensions
ST: Stroke
ME: Mechanical end
SE: Stroke end
(Note) When performing a return to origin, the rod moves to the ME, so be careful not to let it interfere with surrounding objects.
Note: Make sure to secure the cable so that the base of the cable does not move.
The cable can be separated and replaced (connected via the connector inside the cable box).
The standard direction for the actuator cable to exit is from the rear.
The cable exit direction (optional) can be changed by changing the direction of the cable box.
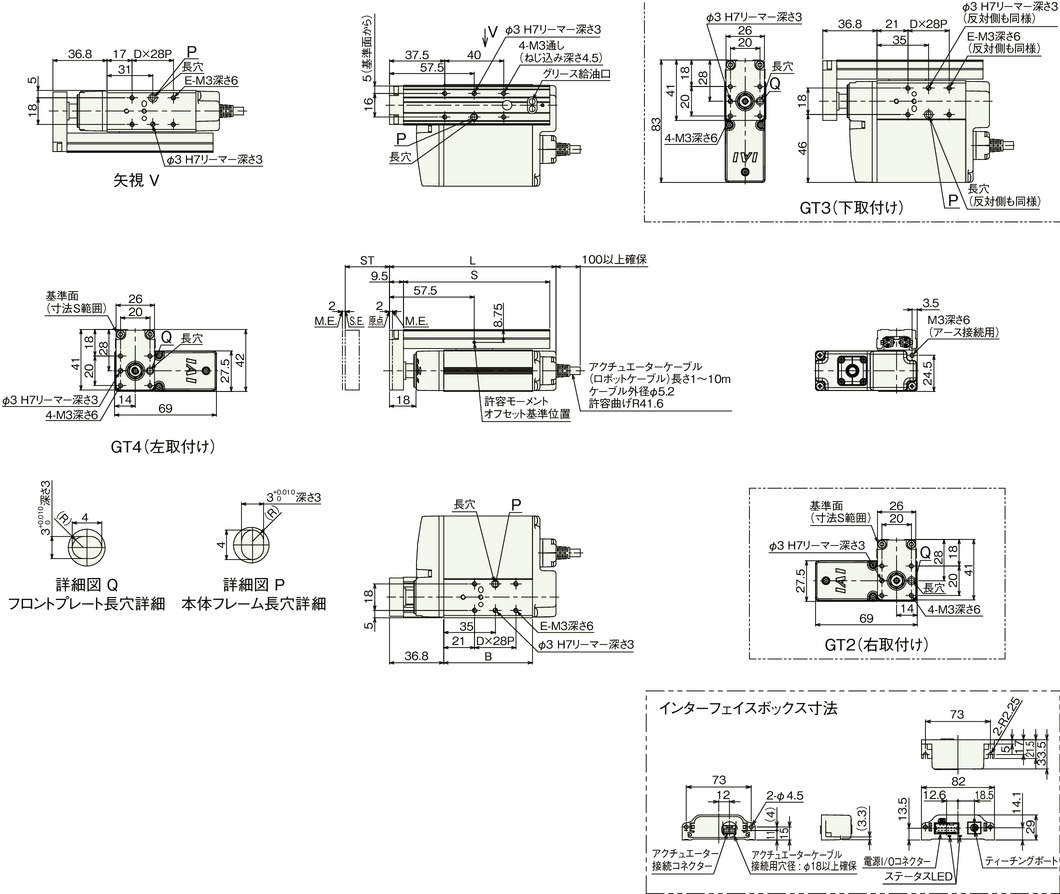
Stroke dimensions
stroke | 30 | 50 | |
---|---|---|---|
L | No brakes | 113 | 133 |
With brake | 158 | 158 | |
B | No brakes | 60.2 | 80.2 |
With brake | 105.2 | 105.2 | |
D | No brakes | 1 | 1 |
With brake | 2 | 2 | |
E | No brakes | 4 | 4 |
With brake | 6 | 6 | |
S | 99.2 | 119.2 |
Mass by stroke
stroke | 30 | 50 | |
---|---|---|---|
Mass (kg) |
No brakes | 0.46 | 0.52 |
With brake | 0.63 | 0.65 |
Cable exit direction option (optional)
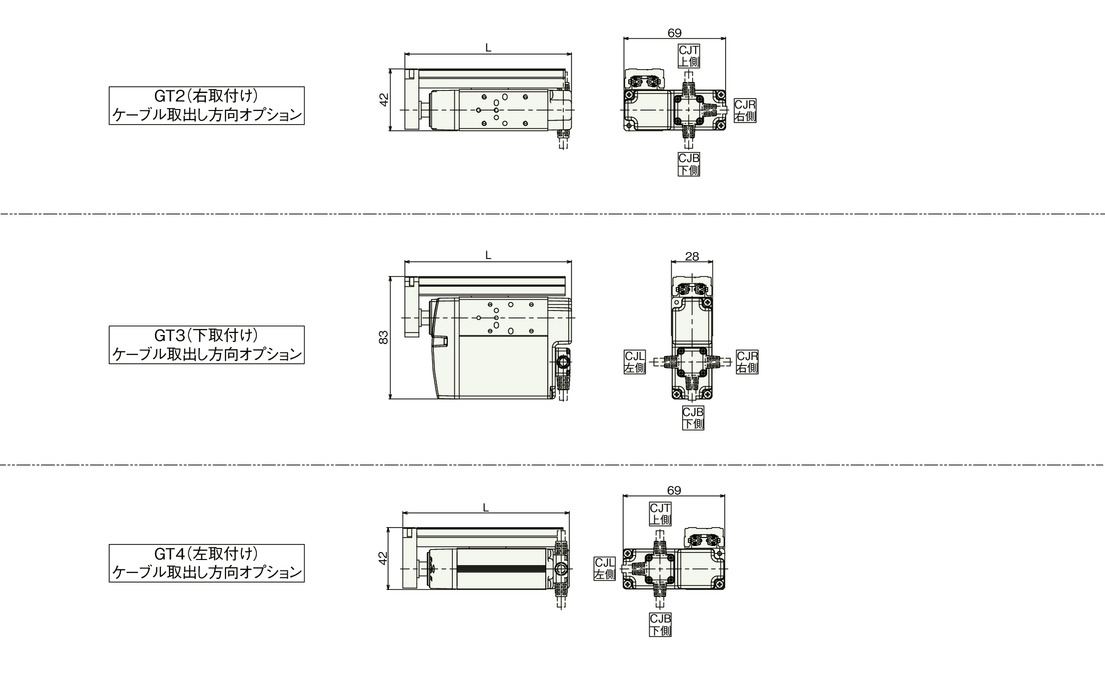