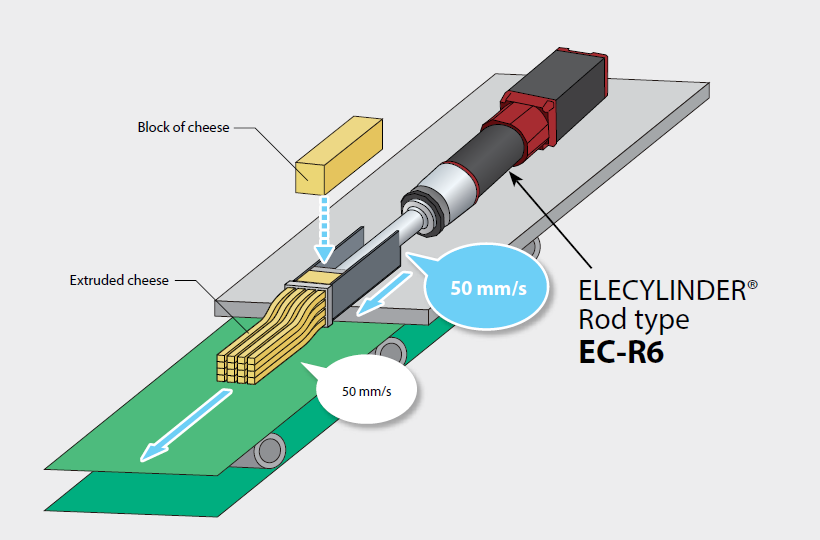
 2   Extruding cheese to cut into string-like thin shapes.
 3   Placing cut cheese on the conveyor belt and sending them to the next process.
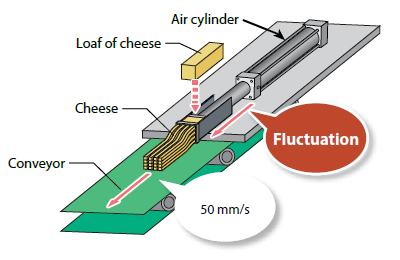
Past problems
Adjustment time before operation startup: 30 minutes / day
It took a long time to adjust the speed controller to synchronize the cheese extruding speed with the conveyor belt.
Wasted product: 10 pieces / day
Even after adjustments, products were wasted due to fluctuation of the air source pressure.
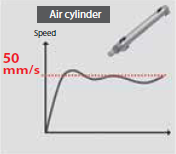
Time for adjusting the speed controller: 30 minutes / day
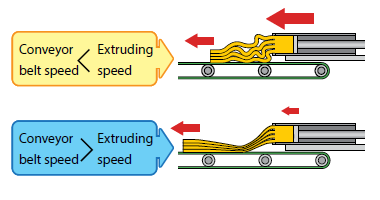
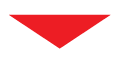
After installation of an ELECYLINDER®
Reduced labor cost
Adjustments for cheese extruding speed is no longer needed when starting operation, reducing the adjustment time from 30 minutes to zero.
As a result, annual labor cost is reduced by $2,100.
Zero products wasted
By using an ELECYLINDER, no defective products are made, reducing the cost from $10 /day to zero.
Annual savings in wasted products is $2,400.
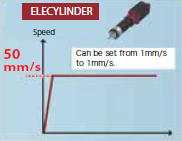
Once the speed is set, it will always be constant. Zero minute / day
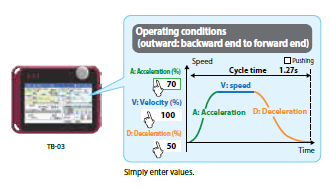
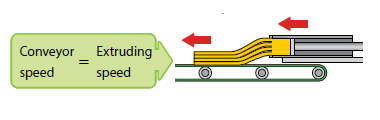
As a result, cheese can be cut into thin string-like shapes uniformly.
Conditions
Material cost (block of cheese) |
$1 / piece |
Conveyor belt speed |
50 mm/s |
Number of extrusions | 1,200 times / day |
Wasted products (conventional device) | 10 pieces / day |
Number of workers | 1 |
Labor Cost | $18 / hour |
Annual operation days | 240 days |
Details
Adjustment time is reduced from 30 minutes to 0.
30 minutes x $18/hour x 240 days = $2,160/year
Wasted products have been reduced from 10 pieces
to zero per day.
10 pieces x $1 (material cost per piece) x 240 days
= $2,400 /year.
*Exchange Rate: 1(USD)=100(Japanese Yen)