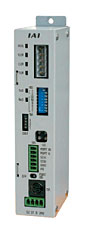
The gateway unit is a conversion unit for connecting a ROBO Cylinder controller to a field network such as DeviceNet or CC-Link. Connect a gateway unit to your field network, and link the gateway unit and each controller via serial communication (RS485).
Numerical data such as coordinates, speeds, accelerations and current values can be sent and received between the network master (PLC) and controller by means of I/O-level communication.
From single-axis controllers with basic programmability to multi-axis models able to handle the most complex applications, with IAI you can pick and choose from an extensive line of models.
Features |
- Move the actuator by specifying positions from a PLC via network.
- Perform push-motion operation via network.
- Operate the actuator by directly sending the target position, speed, acceleration/deceleration and positioning band as numerical values from a PLC.
- Read the current actuator position and various signals using a PLC.
- Connectable to a maximum of 16 axes.
|
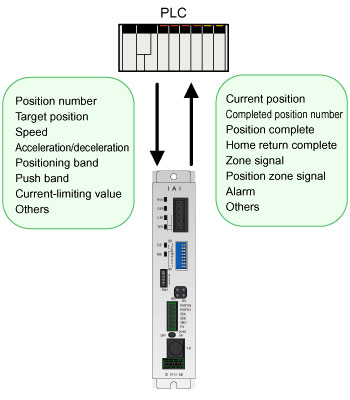 |
Functions |
One of the following three operation models can be selected.
- Position-number specification mode
Input target positions, speeds, accelerations/decelerations, positioning bands and other settings to the controller in advance as position data, and specify a desired position number via network, just like you do with PIO signals, to move the actuator. A maximum of 64 positioning points can be set. Various status signals can be read using a PLC.
- Positioning-data specification mode
Specify a desired target position, speed, acceleration/deceleration, positioning band, push band, current-limiting value, etc., directly as numerical values to move the actuator or cause it to perform push-motion operation. Various status signals can be input/output and current signals can be input/output and current position data read using a PLC.
- Simple direct/position-number specification mode
Call desired position data except for a target position (by specifying an applicable position number), and specify only a target position as a numerical value, to move the actuator. A maximum of 512 positioning points can be set.
Go to:
 |